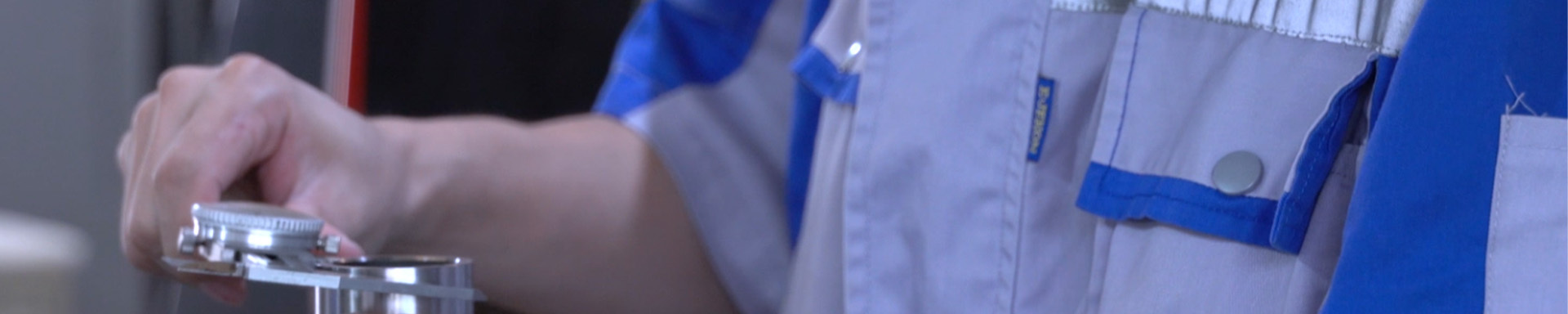
Ứng dụng của hợp kim Coban trong môi trường nhiệt độ cực thấp
2025-07-04 09:00In the field of ultra-low temperature engineering, the materials of equipment accessories must have mechanical stability, embrittlement resistance and corrosion resistance at extreme temperatures. Cobalt-based alloys have excellent comprehensive performance in ultra-low temperature environments due to their unique composition and microstructure. They have become key materials for spare parts in aerospace, LNG, superconducting technology and other fields.
Cobalt Alloys
Cobalt alloys are based on cobalt, with mainly chromium, tungsten, carbon, and other elements added. The close-packed hexagonal crystal structure of cobalt has excellent toughness at low temperatures, and the dense Cr2O3 oxide film can effectively resist corrosion. Tungsten improves the strength of the matrix through solid solution strengthening, while carbon forms high-hardness carbides with chromium and tungsten, which are evenly distributed in the cobalt-based solid solution to form a dddhhhhard skeletondddhhh structure, which provides both wear resistance and toughness. This complex phase structure makes it less prone to embrittlement at ultra-low temperatures and has an outstanding impact resistance.
The Core Advantage of Cobalt Alloys in Ultra-Low Temperature Environments
Cobalt alloys can still maintain high strength and plasticity at -196°C, and the low-temperature toughness of their cobalt-based solid solution effectively inhibits crack propagation. In contrast, ordinary stainless steel is prone to embrittlement due to martensitic transformation at ultra-low temperatures. At the same time, cobalt alloy avoids crystal structure phase change through composition optimization and ensures organizational stability.
In ultra-low temperature media such as LNG, the surface cladding layer of cobalt alloy can resist the corrosive environment containing Cl⁻. For example, a particular LNG butterfly valve uses a cobalt alloy cladding valve body, combined with a cryogenic treatment process, so that the two-way floating structure of the sealing ring can achieve radial dynamic balance sealing, significantly reducing wear and extending service life.
The high hardness carbide of cobalt alloy can effectively resist abrasive wear and erosion wear at ultra-low temperatures. For example, in LNG pump sleeves and sealing rings, the wear resistance of cobalt alloy makes its life 3–5 times longer than that of ordinary materials. In addition, its fatigue resistance can withstand frequent temperature cycles.
Application of Cobalt Alloy in Ultra-Low Temperature Field
Liquefied Natural Gas (LNG) Equipment
Cobalt alloy has become an ideal material for valve sealing surfaces, pump impellers and bearings in the key components of LNG storage tanks, transport ships, and transmission pipelines due to its low temperature and wear resistance. After cryogenic treatment, the sealing components prepared can meet the stringent requirements of low-temperature working conditions, significantly reduce the opening and closing torque of the equipment and extend the service life, effectively ensuring the safe and stable operation of the LNG industry chain.
Space Cryogenic Propulsion System
Cobalt alloy plays a key role in the turbine pumps, valves and pipeline components of liquid hydrogen/liquid oxygen rocket engines. Faced with the extremely low temperature environment of -253℃, its excellent cavitation and thermal shock resistance can ensure that core components such as turbine blades and seals maintain reliable performance under high and low temperature alternating loads. This type of alloy has both high temperature strength and low temperature toughness, and can adapt to the complex thermal-mechanical conditions in the propulsion system.
Superconducting Technology and Cryogenic Engineering
Cobalt alloys have become the preferred material for supporting structures and connecting components due to their low thermal expansion coefficient in the structural design of superconducting magnets and cryogenic refrigeration equipment. This feature makes it form a good thermal match with superconducting materials, effectively reducing the impact of thermal stress in low temperature environments. Even under extremely low temperature conditions of -269℃, its stable mechanical properties can still ensure the reliability and integrity of the equipment structure.
Comparative Analysis of Material Properties
From the performance comparison, cobalt alloys have outstanding performance in hardness, low-temperature toughness, corrosion resistance and wear resistance. Its room temperature hardness can reach 40–60HRC, significantly higher than titanium alloys and stainless steel.
Regarding low-temperature toughness, cobalt alloys have no embrittlement phenomenon at -196℃, titanium alloys can maintain a certain plasticity at -253℃, and ordinary stainless steel is prone to brittle fracture at -196℃.
Cobalt alloys have excellent resistance to Cl⁻ corrosion, titanium alloys have good resistance to oxidizing media, and stainless steel needs to be passivated to improve corrosion resistance.
Regarding wear resistance, cobalt alloys have excellent performance due to carbide strengthening, titanium alloys have moderate wear resistance and rely on surface treatment, and stainless steel has poor wear resistance and is prone to wear problems during use.